Porosity in Welding: Identifying Common Issues and Implementing Best Practices for Prevention
Porosity in welding is a pervasive problem that frequently goes undetected until it causes significant problems with the integrity of welds. In this discussion, we will certainly explore the key elements adding to porosity development, analyze its damaging results on weld efficiency, and discuss the ideal techniques that can be taken on to minimize porosity occurrence in welding procedures.
Typical Sources Of Porosity
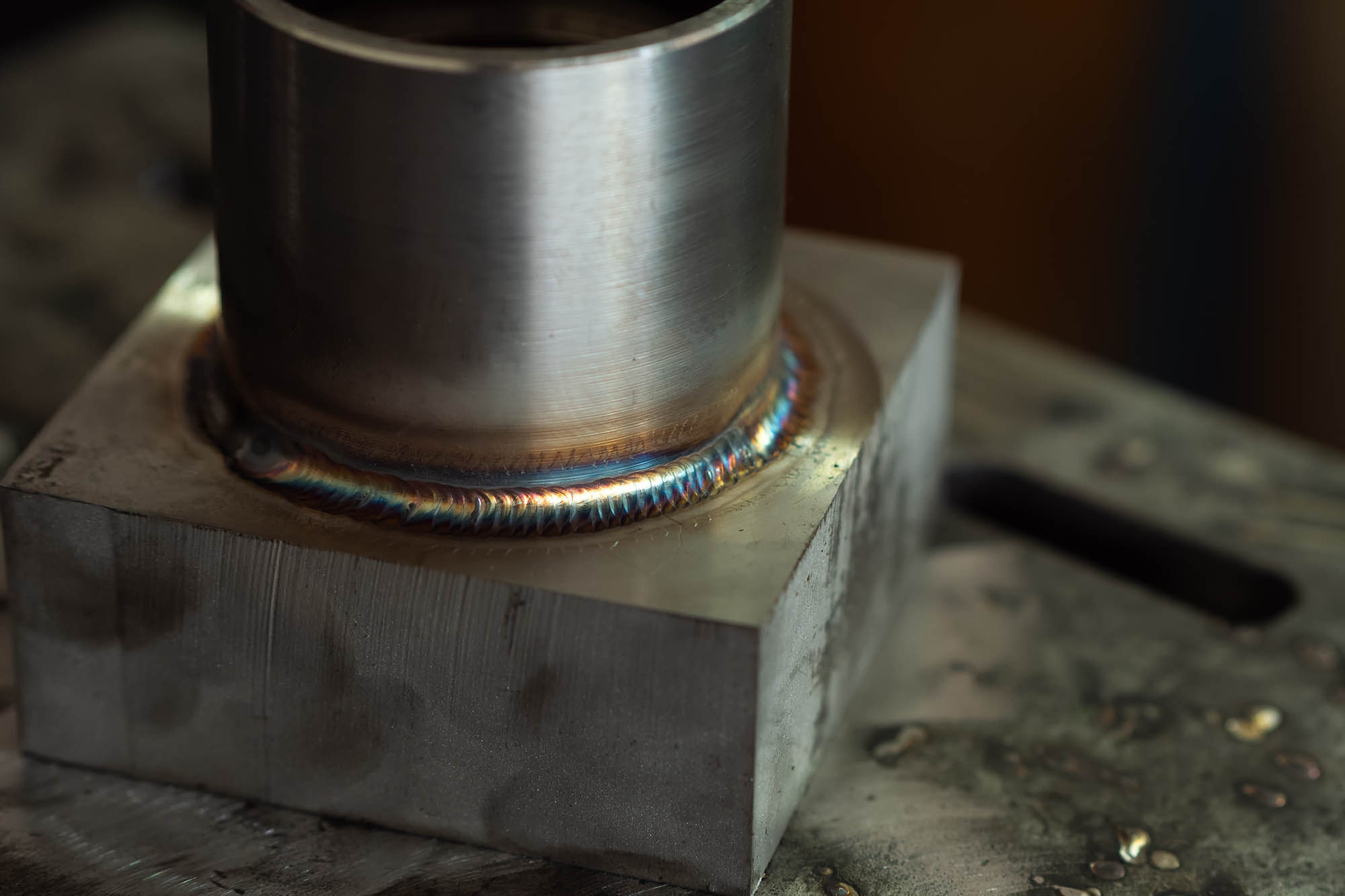
Utilizing dirty or damp filler products can introduce impurities into the weld, adding to porosity concerns. To reduce these typical reasons of porosity, thorough cleaning of base steels, correct securing gas choice, and adherence to ideal welding specifications are vital practices in attaining high-grade, porosity-free welds.
Impact of Porosity on Weld Quality

The existence of porosity in welding can substantially endanger the architectural integrity and mechanical buildings of bonded joints. Porosity creates gaps within the weld metal, compromising its general stamina and load-bearing capability. These gaps work as stress focus points, making the weld much more susceptible to breaking and failing under applied lots. Furthermore, porosity can decrease the weld's resistance to rust and other environmental factors, even more decreasing its durability and performance.
Welds with high porosity levels tend to exhibit reduced influence strength and decreased capacity to deform plastically prior to fracturing. Porosity can impede the weld's capability to effectively send forces, leading to early weld failure and possible safety threats in vital frameworks.
Ideal Practices for Porosity Prevention
To enhance the structural stability and high quality of welded joints, what certain procedures can be carried out to lessen the incident of porosity throughout the welding procedure? Making use of the proper welding strategy for the certain material being welded, such as adjusting the welding angle and gun placement, can better avoid porosity. Normal evaluation of welds and immediate remediation of any kind of problems recognized during the welding process are vital techniques to avoid porosity and produce high-quality welds.
Importance of Appropriate Welding Strategies
Implementing correct welding methods is critical in making sure the structural stability and quality of welded joints, constructing upon the foundation of efficient porosity avoidance redirected here procedures. Welding techniques straight affect the general toughness and durability of the welded framework. One essential aspect of appropriate welding strategies is maintaining the proper warm input. Excessive heat can result in boosted porosity as a result of the entrapment of gases in the weld swimming pool. On the other hand, inadequate warmth might cause insufficient fusion, developing potential powerlessness in the joint. Additionally, making use of the ideal welding parameters, such as voltage, current, and travel rate, is important for accomplishing sound welds with Extra resources very little porosity.
Furthermore, the option of welding process, whether it be MIG, TIG, or stick welding, should straighten with the particular demands of the project to ensure ideal outcomes. Proper cleansing and prep work of the base metal, along with selecting the ideal filler product, are also crucial components of skillful welding techniques. By sticking to these finest practices, welders can decrease the danger of porosity development and create top notch, structurally sound welds.

Evaluating and Quality Control Actions
Testing procedures are essential to spot and prevent porosity in welding, ensuring the toughness and longevity of the last product. Non-destructive testing approaches such as ultrasonic testing, radiographic screening, and aesthetic evaluation are typically utilized to identify potential issues like porosity.
Carrying out pre-weld and post-weld inspections is additionally vital in maintaining quality assurance standards. Pre-weld assessments include verifying the products, devices settings, and sanitation of the workplace to avoid contamination. Post-weld assessments, on the various other hand, examine the final weld for any type of defects, consisting of porosity, and confirm that it satisfies defined standards. Carrying out an extensive quality assurance plan that consists of detailed testing treatments and evaluations is extremely important to decreasing porosity concerns and guaranteeing the total quality of bonded joints.
Conclusion
To conclude, porosity in welding can be a common issue that affects the high quality of welds. By recognizing the usual reasons of porosity and carrying out best techniques for avoidance, such as appropriate welding strategies and screening actions, welders can ensure premium quality and reputable welds. It is necessary to focus on avoidance approaches to reduce the occurrence of helpful resources porosity and maintain the integrity of bonded frameworks.